What is density and density reduction?
Density reduction refers to the mass of a substance per unit volume. It is a measure of how much mass is contained within a given volume of material. The formula for density (ρ) is:
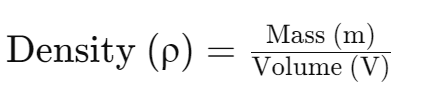
where:
– Mass (m) is the amount of matter in the substance, typically measured in kilograms (kg) or grams (g).
– Volume (V) is the amount of space occupied by the substance, typically measured in cubic meters (m³) or cubic centimeters (cm³).
Density is an intrinsic property of a material and is often expressed in units such as kilograms per cubic meter (kg/m³) or grams per cubic centimeter (g/cm³). Substances with higher densities have more mass packed into a given volume, while substances with lower densities have less mass per unit volume.
Density reduction, on the other hand, refers to the process of decreasing the density of a material. This can be achieved through various methods, such as incorporating lightweight fillers, creating voids or air pockets within the material structure, or optimizing material composition and processing techniques.
The goal of density reduction is to produce materials that are lighter in weight while maintaining or improving their performance characteristics. This can lead to benefits such as increased fuel efficiency, improved handling and maneuverability, enhanced thermal insulation, and reduced material costs. Density reduction is commonly employed in industries such as automotive, aerospace, construction, packaging, and consumer goods to achieve weight savings and optimize material performance for specific applications.
What’s the benefits of density reduction?
Density reduction offers several benefits across various industries and applications. Some of the key advantages include:
1. Weight Savings:
By reducing the density of materials, products become lighter in weight. This can lead to significant weight savings, particularly in applications where weight is a critical factor, such as automotive, aerospace, and transportation industries. Lighter materials require less energy to transport and handle, resulting in cost savings and improved efficiency.
2. Improved Fuel Efficiency:
In industries such as automotive, aerospace, and marine, reducing the weight of vehicles and aircraft can lead to improved fuel efficiency. Lighter vehicles require less fuel to achieve the same level of performance, resulting in lower operating costs and reduced environmental impact due to lower greenhouse gas emissions.
3. Enhanced Performance:
Density reduction can sometimes lead to improvements in material properties, such as thermal insulation, acoustic damping, and vibration absorption. Lightweight materials with optimized properties can offer enhanced performance characteristics compared to their heavier counterparts, leading to improved functionality and user experience.
4. Increased Payload Capacity:
In transportation and logistics, reducing the weight of packaging materials and cargo can increase the payload capacity of vehicles and shipping containers. This allows for more goods to be transported in a single trip, leading to higher efficiency and lower transportation costs.
5. Cost Savings:
Lightweight materials often require fewer raw materials and resources to produce, leading to cost savings in material procurement and manufacturing processes. Additionally, lighter products may incur lower transportation and handling costs, further contributing to overall cost savings throughout the product lifecycle.
6. Environmental Benefits:
Density reduction can contribute to environmental sustainability by reducing energy consumption, greenhouse gas emissions, and resource depletion. Lightweight materials require less energy to produce, transport, and use, leading to lower environmental impact and reduced carbon footprint.
7. Design Flexibility:
Lightweight materials offer design flexibility and versatility, allowing engineers and designers to explore innovative solutions and creative designs. Reduced weight can enable the development of sleeker, more aerodynamic structures and products that offer improved performance and aesthetics.
Density reduction offers a wide range of benefits across industries, including cost savings, improved performance, environmental sustainability, and design flexibility. By leveraging lightweight materials and optimizing product design and manufacturing processes, companies can enhance competitiveness, drive innovation, and meet the evolving needs of consumers and markets.
How to reach the target of density reduction?
Achieving density reduction requires a systematic approach that involves careful consideration of material selection, design optimization, manufacturing processes, and performance requirements. Here are some strategies to reach the target of density reduction:
1. Material Selection:
– Choose lightweight materials: Select materials with inherently low density, such as aluminum, titanium, composites, or polymers. These materials offer high strength-to-weight ratios and can significantly reduce the overall weight of the product.
– Utilize lightweight fillers: Incorporate lightweight fillers such as expandable microspheres, hollow glass or ceramic microspheres, or natural fibers into composite materials to reduce density while maintaining or improving mechanical properties.
2. Design Optimization:
– Design for lightweight: Use advanced design techniques such as topology optimization, lattice structures, or biomimicry to optimize the shape and geometry of components for maximum strength and minimum weight.
– Reduce material thickness: Minimize material thickness in non-critical areas while maintaining structural integrity and performance. This can be achieved through topology optimization, finite element analysis, or generative design approaches.
– Use efficient structural configurations: Employ efficient structural configurations such as trusses, ribs, or honeycomb structures to achieve high stiffness and strength with minimal material usage.
3. Manufacturing Processes:
– Employ additive manufacturing: Utilize additive manufacturing (3D printing) technologies to produce lightweight, complex geometries with optimized material distribution. Additive manufacturing enables the creation of lightweight structures with reduced material waste and assembly complexity.
– Optimize molding processes: Implement advanced molding techniques such as resin transfer molding (RTM), vacuum infusion, or compression molding to produce lightweight composite parts with precise control over fiber orientation and resin content.
4. Performance Requirements:
– Conduct material characterization: Perform comprehensive material testing and characterization to assess the mechanical, thermal, and acoustic properties of lightweight materials and ensure they meet performance requirements.
– Balance weight reduction with performance: Strike a balance between weight reduction and performance requirements by optimizing material selection, design parameters, and manufacturing processes to achieve the desired performance targets while minimizing weight.
5. Lifecycle Considerations:
– Consider end-of-life recycling: Evaluate the recyclability and sustainability of lightweight materials to minimize environmental impact throughout the product lifecycle. Choose materials that are recyclable or biodegradable and incorporate circular economy principles into product design and manufacturing processes.
6. Collaboration and Innovation:
– Foster collaboration: Collaborate with suppliers, partners, and research institutions to explore new materials, technologies, and design approaches for achieving density reduction.
– Foster innovation: Encourage a culture of innovation within the organization by incentivizing creativity, rewarding experimentation, and investing in research and development initiatives focused on lightweighting and sustainability.
By implementing these strategies and adopting a holistic approach to density reduction, companies can achieve significant weight savings, improve product performance, and enhance sustainability across a wide range of industries and applications.
What industry will demand density reduction?
Density reduction is a critical requirement across various industries where weight reduction can lead to significant benefits in terms of performance, efficiency, and cost savings. Some of the key industries that demand density reduction include:
1. Automotive:
The automotive industry is constantly striving to reduce vehicle weight to improve fuel efficiency, increase range in electric vehicles, enhance performance, and meet stringent emissions regulations. Lightweight materials and components are used extensively in vehicle bodies, chassis, interiors, and powertrain systems to achieve these objectives.
2. Aerospace:
In aerospace and aviation, reducing aircraft weight is essential for improving fuel efficiency, increasing payload capacity, extending range, and enhancing overall performance. Lightweight materials such as composites, titanium, and aluminum alloys are widely used in aircraft structures, engines, and components to achieve weight savings while maintaining strength and durability.
3. Transportation:
Beyond automotive and aerospace, density reduction is also important in other transportation sectors such as rail, marine, and commercial vehicles. Lightweight materials and components help reduce energy consumption, increase load capacity, and improve operational efficiency in various transportation applications.
4. Construction:
In the construction industry, lightweight materials play a crucial role in reducing the weight of building structures, improving energy efficiency, and enhancing construction speed and safety. Lightweight concrete, insulation materials, and composite panels are commonly used to achieve these objectives in residential, commercial, and infrastructure projects.
5. Packaging:
In the packaging industry, lightweight materials are used to reduce packaging weight, minimize material usage, and optimize logistics and transportation costs. Lightweight packaging materials such as foams, plastics, and paperboard help reduce packaging waste and environmental impact while ensuring product protection and safety.
6. Consumer Electronics:
In consumer electronics and appliances, reducing product weight is important for improving portability, user comfort, and energy efficiency. Lightweight materials such as plastics, composites, and lightweight metals are used to manufacture smartphones, laptops, tablets, and household appliances.
7. Sports and Recreation:
Lightweight materials are widely used in sports equipment and recreational products to enhance performance, maneuverability, and user experience. Lightweight materials such as carbon fiber, aluminum alloys, and composite materials are used in bicycles, skis, snowboards, golf clubs, and athletic footwear.
8. Medical Devices:
In the medical industry, lightweight materials play a crucial role in the development of medical devices and implants. Lightweight materials such as titanium, polymers, and bioresorbable materials are used to manufacture surgical instruments, implants, prosthetics, and medical equipment to improve patient comfort and mobility.
Density reduction is a key requirement in industries where weight reduction can lead to improvements in performance, efficiency, and sustainability. By leveraging lightweight materials and innovative design and manufacturing techniques, companies can achieve significant benefits across a wide range of applications and industries.
How is the trend of density reduction in future?
The trend of density reduction is expected to continue and even accelerate in the future, driven by several factors and technological advancements. Here are some key trends that are likely to shape the future of density reduction:
1. Demand for Lightweight Vehicles:
With the growing emphasis on fuel efficiency, emissions reduction, and electric mobility, the automotive industry will continue to prioritize lightweighting efforts. Manufacturers will increasingly adopt advanced materials, such as carbon fiber composites, aluminum alloys, and high-strength steel, to reduce vehicle weight while maintaining safety and performance standards. Additionally, the development of lightweight batteries and electric drivetrains will further drive the adoption of lightweight materials in electric vehicles.
2. Advancements in Materials Science:
Ongoing research and development in materials science will lead to the discovery and development of new lightweight materials with improved properties and performance characteristics. Nanomaterials, biomimetic materials, and advanced composites will play a significant role in achieving weight reduction goals across various industries. Furthermore, advancements in additive manufacturing and nanotechnology will enable the production of complex lightweight structures with optimized material distribution.
3. Integration of Lightweight Materials in Aerospace:
In the aerospace industry, the demand for lightweight materials will continue to grow as aircraft manufacturers strive to reduce fuel consumption, increase range, and improve operational efficiency. Advanced composite materials, such as carbon fiber-reinforced polymers and ceramic matrix composites, will see increased adoption in aircraft structures, engines, and components. Moreover, the development of additive manufacturing technologies for aerospace applications will enable the production of lightweight, complex components with reduced lead times and material waste.
4. Sustainable Lightweight Solutions:
Sustainability considerations will drive the development of lightweight materials and solutions that minimize environmental impact throughout their lifecycle. Recyclable, bio-based, and biodegradable materials will gain prominence as companies seek to reduce carbon emissions, minimize resource consumption, and promote circular economy principles. Additionally, the use of lightweight materials in energy-efficient buildings, renewable energy systems, and sustainable transportation solutions will contribute to the transition towards a more sustainable future.
5. Digitalization and Design Optimization:
Digitalization and advanced simulation techniques will enable engineers and designers to optimize product designs for lightweighting and performance. Virtual prototyping, finite element analysis, and generative design algorithms will facilitate the development of lightweight structures with enhanced strength, stiffness, and durability. Digital twin technologies will enable real-time monitoring and optimization of lightweight components throughout their lifecycle, leading to improved reliability and maintenance efficiency.
6. Regulatory Drivers:
Stringent regulations and emissions standards will continue to drive the adoption of lightweight materials and fuel-efficient technologies across industries. Government policies aimed at reducing greenhouse gas emissions, improving energy efficiency, and promoting sustainable development will incentivize companies to invest in lightweighting initiatives and develop innovative solutions for weight reduction.
Overall, the trend of density reduction will remain a key focus area for industries seeking to improve performance, efficiency, and sustainability in the face of evolving market demands, technological advancements, and regulatory requirements. By embracing lightweight materials, advanced manufacturing techniques, and digitalization tools, companies can unlock new opportunities for innovation, competitiveness, and growth in the future.
For more applications, please check our application sections:
https://www.expandablemicrosphere.com/applications
For more intesting videos, pleast check our Youtube Channel: